Enviromesh System
The Enviromesh wall system is a M.S.E. (Mechanically Stabilized Earth) retaining structure fabricated from continuous double twisted PVC coated mesh panel with a vegetated matting enclosed with a mesh reinforcement backing on the fascia. More material specifications are listed below. This monolithic design using this quality mesh cloth allows the soil reinforcement and vegetated fascia to offer strength, durability and flexibility. Each unit should be placed in the direction of maximum strength, which is the direction the mesh is woven, lying parallel to the direction of soil stress.
Unit Sizes:
(length) (width) (depth)
variable 6',9',12' 1.5', 2',3'
The Enviromesh system (shown below) utilizes straight wire support brackets to support the front facing during soil placement. The wire bracket is simply connected as shown to the locater wire placed on the base reinforcement panel. Style two detail.
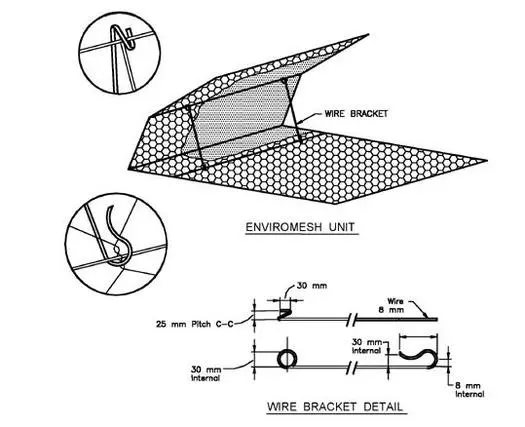
Enviromesh MSE Wire Wall System
PVC Wire Mesh
Polyvinyl chloride coated galvanized steel wire, Class 3, Finish 5, Soft, in accordance with ASTM A641.
Zinc coated in accordance with ASTM A641, Class 3, tested in accordance with ASTM A90.
Polyvinyl Chloride Coating - All wire used in the fabrication of the base units and in wiring operations during construction shall, after zinc coating, have extruded onto it a coating of polyvinyl chloride, otherwise referred to as ÒPVCÓ. The coating shall be gray in color unless otherwise specified. The PVC coating shall be of normal thickness 0.60 mm and shall be capable of resisting deleterious effects of salt spray, UV rays and abrasion. It shall not show any significant material difference in its initial characteristics after 3,000 hours accelerated exposure according to ASTM 8117, ASTM D1499 and ASTM G23, and after 200 cycles according to ASTM Method D1242, Method B.
Wire core for mesh- 2.7mm
Finish - 3.7mm (wire plus PVC coating)
Wire core for selvedge - 3.4mm
Finish - 4.4mm (wire plus PVC coating)
Wire core for lacing - 2.2mm
Finish - 3.2mm (wire plus PVC coating)
Mesh opening: Nominal 8x10 cm
Tensile strength for wire to be in accordance with ASTM A641, Soft.
Tensile strength for PVC mesh to be 42.3kn/m minimum (pulled parallel to wire twists)
Galvanized Reinforcement Panel
Galvanized mesh panel shall be manufactured and galvanized according to Specification stipulated in Section A.1.
Tolerances
Wire - Tolerances on the diameter of all wire in the above paragraphs shall be permitted in accordance with ASTM A641, Table 3.
Units - Tolerances of plus or Minus 5% on the width, height, and length of the unit shall be permitted.
Fabrication
Units shall be made from non-raveling, double twisted hexagonal wire mesh. The mesh will have the ability to resist pulling apart at the twists or connections forming the mesh when a single wire in a mesh section is cut.
Units shall be of single piece construction. They shall be fabricated so that the fold back, fascia and base are continuous and made from the same panel with no joints.
Wire Mesh Tests
Elongation - Test shall be made on the wire before fabrication of the units on a Sample twelve inches long. Elongation shall not be less than 12%.
Strength - The wire mesh shall not rupture when subjected to a load of 26.7KN applied as follows:
Clamp a section 2m long, not less than 1m wide including selvedge bindings, for 1m along the width, or in the middle widths greater than 1 feet, with excess falling free on each side.
Apply tension to elongate the section 10%.
Apply the load, 26.7KN as stated above, to a 0.093 square meter section located approximately in the center of the sample between the clamps. The direction of the load should be perpendicular to the tension force direction and be applied with a circular ram bead with the edges beveled or rounded to prevent cutting the wires.
Structural Backfill
The structural backfill shall consist of a good quality granular selected soil. It shall be free draining and posses a high angle of internal friction (greater than 26-30). Compaction shall satisfy the local specifications for highway construction. Gradation limits for the structural fill shall not be 10% finer than 0.02mm, with a 100% by weight finer than 6.0 mm. However, such that a maximum of 15% by weight shall pass the #200 sieve: a maximum of 40% shall pass the #40 sieve; and maximum particle size of 250 mm may be used.
Assembling
Units shall be assembled and erected according to manufacturer's instructions and project specifications. Units are supplied folded flat and packed in bundles. Single units shall be removed from the bundle, unfolded on a hard flat surface, and have all kinks and bends worked out before assembly. The erosion control vegetated blanket shall be placed flush to the fascia on the interior portion of the unit such that there is a 12.5 cm overhang on the top and bottom and folded back towards the embedment length. The galvanized reinforcing mesh shall then be placed over the erosion control vegetated blanket in alignment with the fascia. Fasteners shall be used to connect the PVC mesh fascia to the galvanized mesh through the erosion blanket. The galvanized fasteners shall be spaced 5 cm from the top and bottom edge of the reinforcing panel and at the midpoint of the fascia and shall be spaced horizontally at 25 cm on center.
Wire brackets constructed according to the detail provided and manufacturer's recommendation shall then be placed on one meter centers in the interior behind the galvanized backing. The brackets shall be connected to the PVC mesh body in the manner shown in the detail provided for the fascia and the based reinforcement panel. There shall be a locater wire on the base panel to indicate the location of attachment for the bracket.
Installation And Placement
The assembled units are carried to the job site and placed in their proper location according to the contract drawings. For structural integrity, the adjoining empty units must be securely joined together using an approved fastener spaced at 25 cm on center for vertical joints and 60 cm on center for horizontal joints.
Structural backfill shall be placed in maximum of 0.3m lifts with a minimum 95% compaction. Structural backfill within one meter of the fascia shall be hand compacted using a hand tamper or vibrator.
Once the first layer of units has been installed and the backfill is compacted to the proper height, the next units shall be placed on top of the first layer. The PVC mesh of the second layer shall then be connected to the overhang of the unit directly below it using the technique in Section F, paragraph F.1.
The final lift shall have the first 1.5 meters behind the fascia compacted first using the technique in paragraph G.2. The fold back shall then be secured to the Embedment mesh approximately 1.5 meters behind the fascia using PVC coated tie Wire. Connections shall be spaced on 25 cm and shall be connected so that the free ends have a minimum of three full turns around the body of the mesh.
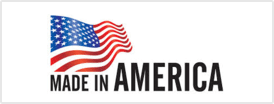
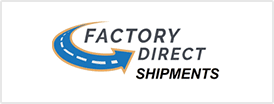
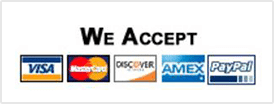
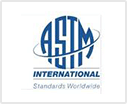
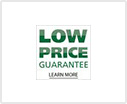
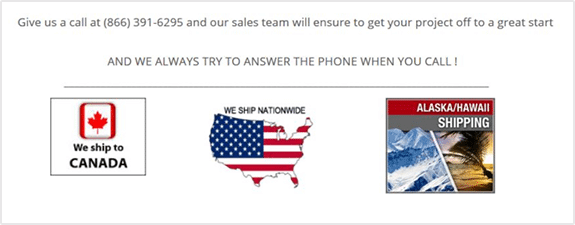